Epoxy a world of creativity
Shall be a multi-component solvent free, epoxy resin coating system supplied in preweighed packs ready for on-site mixing and use.
The cured film shall form a very hard coating with excellent adhesion to clean substrate; the coating shall cure to a semi-gloss, impervious finish which is easily cleaned. Color shall be selected from range of manufacturer’s standard colors by the Engineer.
The used coating shall be of the following properties:
- Hard wearing, durable and requires low maintenance costs
- High resistance to industrial chemicals.
Technical properties :
- Compressive Strength: 55 N/ mm2 .
- Tensile Strength: 20 N/mm2 .
- High abrasion resistance C.
The coating shall be applied in two coats each of 250-microns dry film thickness. D. For exposed areas to sunlight, cover the epoxy paint system with two layers of polyurethane of 200-micron thickness DFT each.
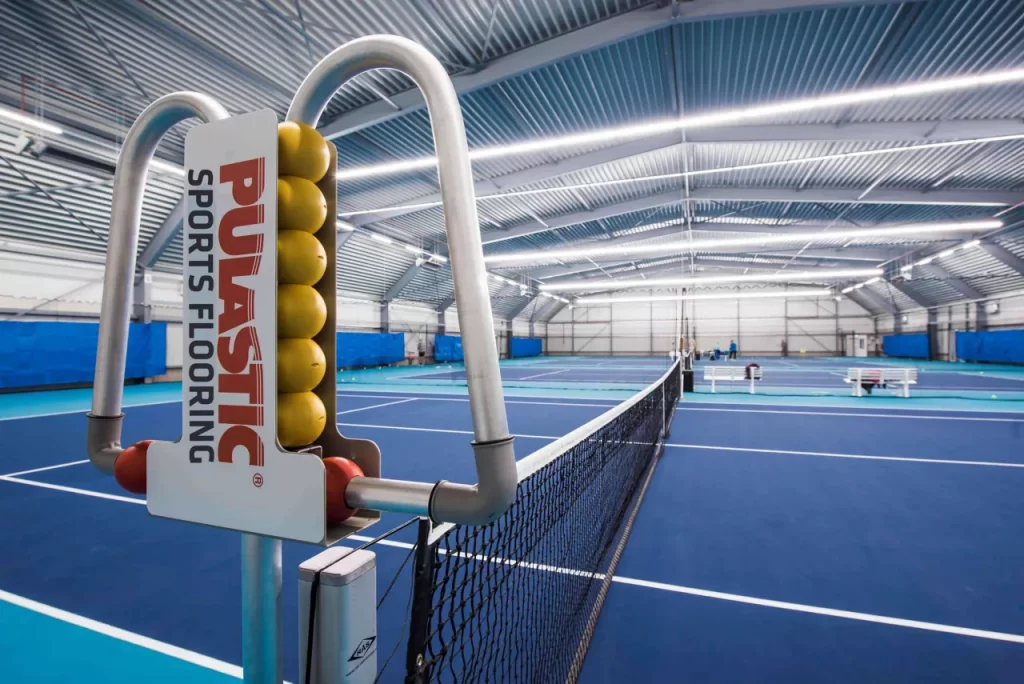
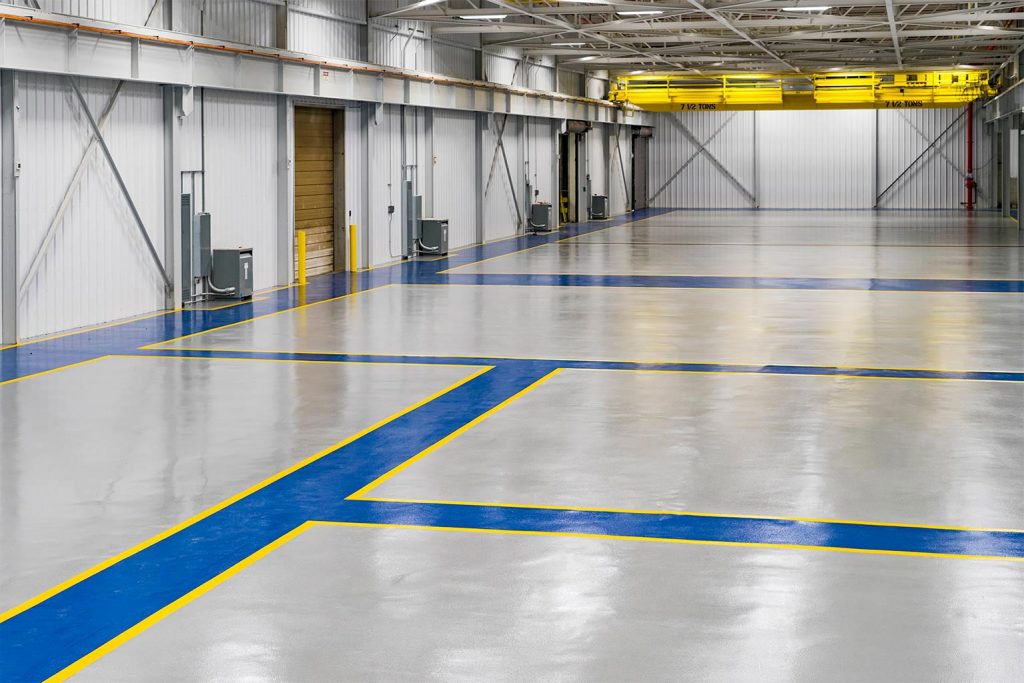
Execution
Preparation:
A- general: Prepare and clean substrate according to resinous flooring manufacture : r’s written instructions for substrate indicated.
Provide clean, dry, and neutral substrate for resinous flooring application.
B-Cement-Based Substrates: Provide sound concrete surfaces free of laitance, glaze, efflorescence, curing compounds, form-release agents, dust, dirt, grease, oil, and other contaminates incompatible with resinous flooring.
- Roughen concrete substrates as follows: a. Shot-blast surfaces with an apparatus that abrades the concrete surface.
- Comply with technicals specification requirements.
- Repair damaged and deteriorated concrete according to resinous flooring.
d.Use patching and fill material to fill holes and depressions in substrates according to manufacturer’s written instructions.
- Treat control joints and other nonmoving substrate cracks to prevent cracks from reflecting through resinous flooring according to manufacturer’s written recommendations.
- Treat control joints and other nonmoving substrate cracks to prevent cracks from reflecting through resinous flooring according to manufacturer’s written recommendations.
Application
- General: Apply components of resinous flooring system according to manufacturer’s written instructions to produce a uniform, monolithic wearing surface of thickness indicated.
- Coordinate application of components to provide optimum adhesion of resinous flooring system to substrate and optimum intercoat adhesion.
- Cure resinous flooring components according to manufacturer’s written instructions.

Prevent contamination during application and curing processes.
- At substrate expansion and isolation joints, provide joint in resinous flooring to comply with resinous flooring manufacturer’s written recommendations.
- Apply joint sealant to comply with manufacturer’s written recommendations.
- Apply primer over prepared substrate at manufacturer’s recommended spreading rate.
- Apply reinforcing membrane to substrate cracks.
- Integral Cove Base: Apply cove base mix to wall surfaces before applying flooring.
- Apply self-leveling slurry body coat(s) in thickness indicated for flooring system.
- Broadcast aggregates and, after resin is cured, remove excess aggregates to provide surface texture indicated.
- Apply troweled or screeded body coat(s) in thickness indicated for flooring system. Hand or power trowel and grout to fill voids. When cured, sand to remove trowel marks and roughness.

9. Apply grout coat, of type recommended by resinous flooring manufacturer to fill voids in surface of final body coat and to produce wearing surface indicated.
10.Apply topcoat(s) in number of coats indicated for flooring system and at spreading rates recommended in writing by manufacturer.